Share
Pin
Tweet
Send
Share
Send

The form
First, decide what you want to cast. As I said, I will pour the figurine. Need to make a foam mold. I use plain white polystyrene, but I advise you to find polystyrene, and both are sold in hardware stores.
Nichrome cutter
But to cut such a foam with an ordinary knife is almost impossible. Let's make a small simple nichrome cutter for polystyrene. You will need:
- Nichrome wire.
- Two chopsticks for sushi.
- Two push pins.
- Cardboard.
- Two wires.
We take a cardboard 5 * 6 cm and on both sides with tape we attach sticks for sushi.

Now insert the buttons into the sticks, but not completely.

Next, we stretch nichrome and wind the wires. And stick the buttons completely. I attached a USB cable to the wires. Now insert USB into the charger from your phone. The wire is hot and less often polystyrene is like butter!


Now we cut out the necessary shapes and with the help of PVA or, like me, hot-melt adhesive, we fasten them as needed.


Also cut the sprues and also glue them.

A few words about the crucible
Metal needs to be melted in something. This is something called a crucible. I made it out of a pipe. I sawed off 40 mm from a steel pipe with a diameter of 90 mm and walls of 2 mm. This height will be a crucible. A steel pancake was welded to the bottom. A handle from a steel corner is welded to the side, but it is better not to take this handle with your bare hands. A triangular cutout is made on the side and a spout is welded from a steel triangle bent in the middle.

Casting
Next, insert the foam molds in the sand so that the tops of the gates stick out of the sand. Near the sprues you need to make small craters of wet sand. But I did not really like this option. Instead of wet sand, I used large nuts.
Now we throw aluminum cans, or any aluminum that you have, into the crucible, melt the hearth and melt. Various slag will accumulate on top (paint on banks, dust, etc.). If possible, it should be removed.

Next, pour aluminum into the gate, the molten metal should appear in the second gate. After about five minutes, the workpiece can be pulled out of the sand and cooled in cold water.
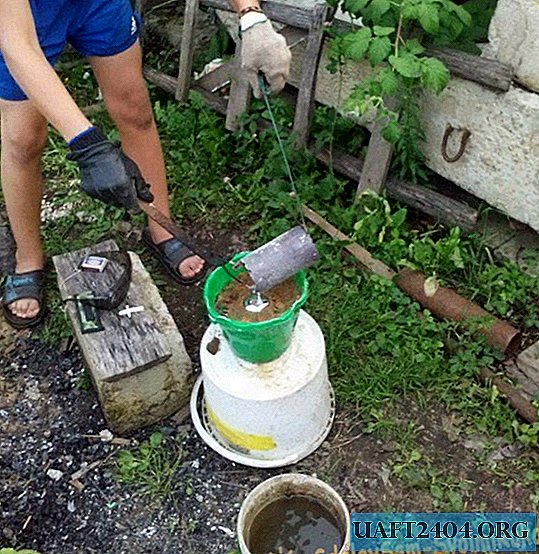
In the photo is an old crucible. It is made of pipe with a diameter of 60mm and a height of 120mm. A steel pancake and a small buttonhole are also welded to the bottom to hook the crucible with wire. Two more lapels are welded on top and a steel wire is stretched. It turned out like a bucket.
If everything has spilled as we proceed to the bench work. Non-ferrous metals are quite soft. We saw off the sprues with a hacksaw and file it, after a minute the result is something like this:

I do not pretend to quality, my goal is to tell you about various techniques.
But if you need accurate casting, it is better to use silicone molds and plaster. I tried to cast the amulet with the head of a cat, but it spilled badly. Maybe this is due to insufficient temperature, but in any case, gypsum forms are much better. Foam forms use for simple models.

Share
Pin
Tweet
Send
Share
Send